Изделия из ДПК (древесно-полимерного композита) активно используются в сфере строительства и отделки. Они стали достойной альтернативой натуральному дереву, обладая при этом более доступной стоимостью и продолжительным сроком службы. Широкая цветовая палитра, большое разнообразие профилей и габаритов – все это дает возможность подобрать панели, подходящие для самых разных проектов. Но как происходит процесс изготовления изделий из ДПК? Какие компоненты нужны для создания качественной террасной доски и в какой последовательности производятся работы? Обо всем по порядку поговорим в нашей статье.
Каковы сферы применения изделий из ДПК? Из этого материала производят:
- доски для использования в наружных и внутренних работах;
- несущие элементы для легких одноэтажных конструкций;
- оконные и дверные рамы;
- облицовочные панели для автомобилей;
- предметы мебели.
Очевидно, что этот материал крайне востребован. Можно предположить, что спрос на него будет только расти. Следовательно, всегда будет актуальной продукция надежных производителей, которые строго следуют технологии производства ДПК.
Материалы и сырье
Под понятием «древесно-полимерного композита» подразумевается сочетание нескольких компонентов, каждый из которых мы рассмотрим в деталях. Правильный их выбор и четкая последовательность работ – гарантия высокого качества конечного изделия.
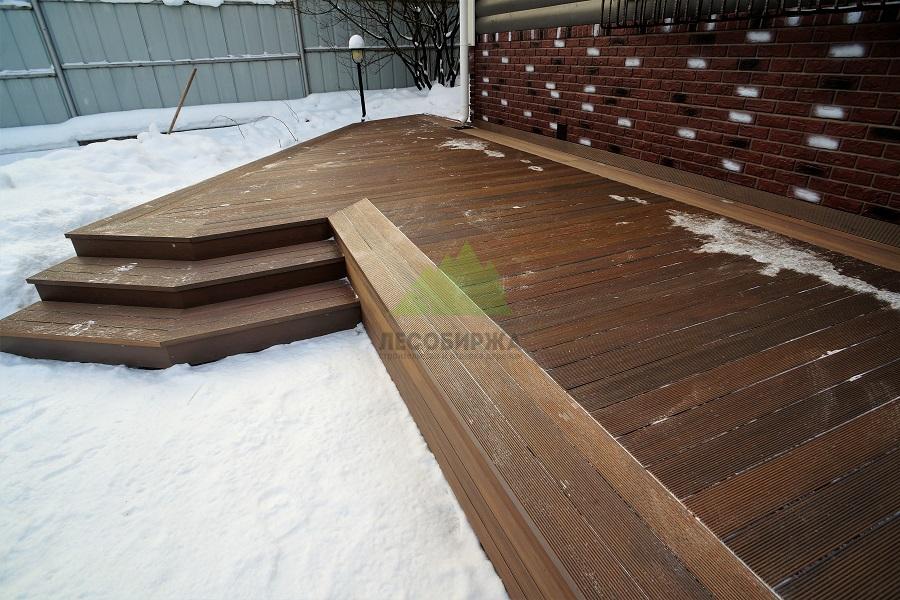
Фото 1. Терраса из ДПК
Древесная мука
Основной компонент (или наполнитель), который используется для производства ДПК, – это древесная мука. Как ее получают? Опилки, появившиеся в результате деревообработки, дополнительно измельчают до определенных размеров. Чем мельче крупицы муки, тем более ровной и гладкой выйдет структура изделия. Затем их просеивают, чтобы не оставалось крупных частиц, и тщательно сушат. Оптимальный показатель влажности для древесной муки – 3-5%. При таком уровне содержания воды конечный продукт получается наиболее качественным.
Полученная мука отличается высокой гигроскопичностью, то есть склонностью впитывать влагу из окружающей среды. По этой причине сырье нужно хранить в максимально сухих помещениях и непродолжительное время. Идеальный вариант – это производство древесной муки на том же предприятии, где будет изготавливаться ДПК.
Какие породы древесины используются для этой цели? Чаще всего используются береза и лиственница. Почему именно они?
- И в одном, и в другом случае мука приобретает светлый, почти белый оттенок. Это облегчает придание материалу определенного цвета в дальнейшем.
- В обеих породах содержится минимум смол. Благодаря такому составу снижается выделение газов в ходе нагревания. В противном случае производство доски было бы сильно затруднено.
Если же используются представители хвойных пород, мука обретает близкий к желтому оттенок. Причем он будет становиться все более выраженным, поскольку смолы будут выгорать из-за высоких температур. Более того, при работе с такой мукой значительно повышается выделение дыма. Это обстоятельство при отсутствии контроля может снизить качество полученного продукта.
Стоит отметить, что идеально однородным оттенок древесной муки не бывает. Он может отличаться в разных партиях, в соответствии с этим меняется и цвет доски. Такие колебания связаны с различным процентным содержанием муки в ДПК. К тому же древесина склонна к изменениям оттенка под влиянием осадков и солнечных лучей. Как итог, композит может тоже незначительно поменять свой цвет.
Процентное содержание древесной муки в ДПК составляет от 60% до 80%. От этой цифры будут зависеть свойства, качество и стоимость продукции. Например, если доля муки составляет около 60%, панели не будут чрезмерно нагреваться на солнце, но в то же время смогут поглощать достаточно тепла, чтобы обеспечить комфортное передвижение по настилу без обуви. Значительный «плюс» использования измельченной древесины – абсолютное отсутствие риска получить занозу.
Можно встретить производителей, которые вместо древесной муки используют рисовую шелуху. Это удешевляет производство, но и сказывается на качестве продукта. С чем это связано? Мука, изготовленная из этого сырья, не обладает направленной структурой. Температурные расширения вдоль такой доски значительно повышаются. Поэтому велик риск столкнуться со следующей проблемой: панели, уложенные летом, к холодному сезону сжимаются и оставляют между собой крупные, заметные зазоры.
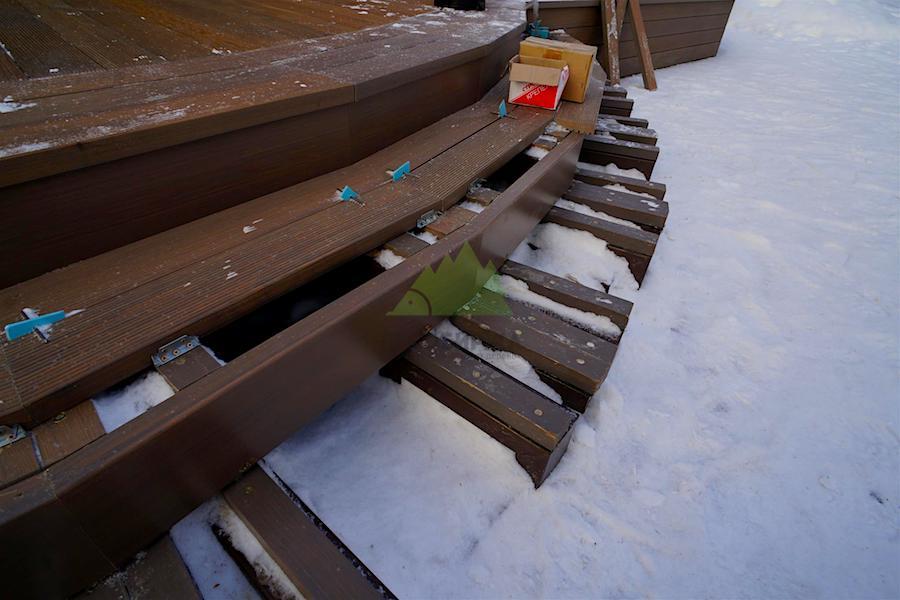
Фото 2. Монтаж террасы из ДПК
Термопластичные полимеры
Следующим компонентом, входящим в состав ДПК, является один из полимеров:
- полиэтилен (ПЭ);
- полипропилен (ПП);
- поливинилхлорид (ПВХ).
Эти элементы претерпевают стадии переработки и очистки, после чего проходят через пресс, где из них формируются некрупные гранулы. Каждое из названных веществ имеет свои характерные особенности, которые влияют на производственный процесс. Логично, что и конечные продукты на их основе будут различаться по свойствам.
Для сравнения: чтобы получить качественную композитную доску с добавлением ПВХ, доля полимера должна составлять от 50% и более. А при работах с ПП достаточно добавить всего лишь 25% этого компонента, и качество изделия не пострадает.
Отдельного внимания заслуживает процесс производства древесно-полимерного композита с использованием ПЭ. В частности, для изготовления ДПК применяется полиэтилен низкого давления (ПНД). Вещество отличается мощными межмолекулярными связями, что обеспечивает материалу высокую прочность и износостойкость. Кроме того, композит с ПНД в составе получается более пластичным и устойчивым к колебаниям температур. Его допустимо использовать во всех климатических зонах, поскольку диапазон температуры, которую он выдерживает, составляет от -45°С до +75°С. Описание работ в данной статье будет связано именно с этим полимером.
Важно знать, что некоторые производители прибегают к использованию «вторичного» полиэтилена, то есть переработанных пластиковых отходов. Конечно, готовый ДПК с таким составом имеет низкую стоимость. Но о его достойном качестве и уровне безопасности говорить не приходится. Со временем композитная доска из вторсырья может сильно пострадать от окисления или под воздействием ультрафиолета. Чтобы как-то компенсировать негативные моменты, придется использовать значительное количество дополнительных присадок, но их высокая стоимость увеличит и цену на изделия из ДПК.
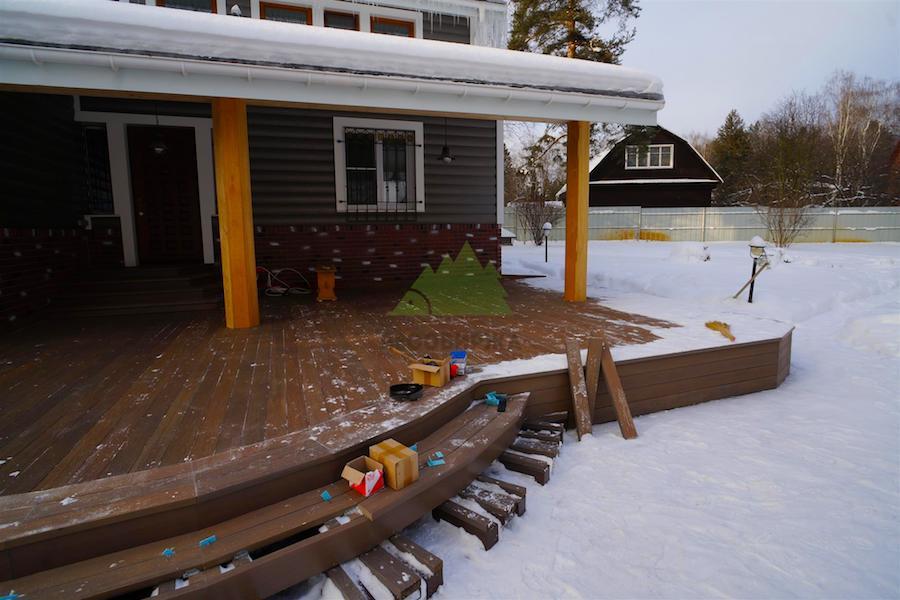
Фото 3. Монтаж ступенек для террасы из ДПК
Минеральные добавки
В роли минерального компонента, который может быть использован при производстве ДПК, выступает карбонат кальция. Это либо технический мел, либо микрокальцит. Какое влияние он оказывает на готовый композит?
- Улучшается структура конечного материала;
- повышается твердость и плотность ДПК;
- доска приобретает высокую влагостойкость.
Также это вещество способно изменить кислотность среды, превращая ее в слабощелочную, за счет чего усиливается противомикробное действие.
Применение карбоната кальция не является обязательным требованием. Многие производители бюджетного ДПК не добавляют этот компонент. Но если ваши финансовые возможности позволяют, вы не пожалеете о приобретении материала с этой минеральной добавкой.
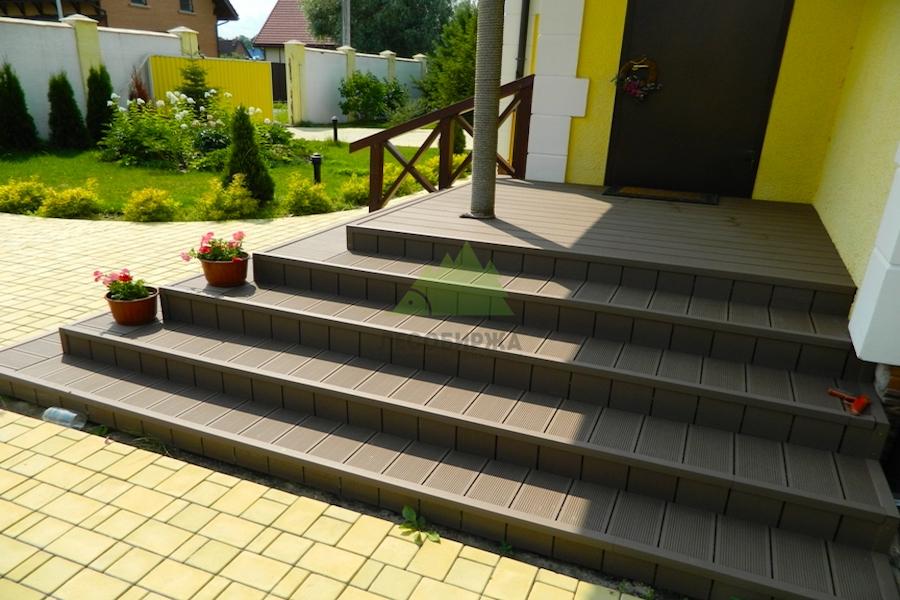
Фото 4. Ступеньки из ДПК
Смазывающие компоненты
Другое название этих веществ – «лубриканты». Они необходимы для того, чтобы процесс экструзии изделий из ДПК осуществлялся без особого «сопротивления». Возможные варианты смазывающих компонентов – это стеариновая кислота или технический воск. Грамотно подобранный лубрикант облегчает процесс изготовления ДПК, повышает его эксплуатационные характеристики и увеличивает продолжительность службы.
Также может использоваться стеарат цинка, но это вещество нередко вступает в реакцию с другими компонентами ДПК. Поэтому его применяют с большой осторожностью.
Связующие агенты (компатибилизаторы)
Без этой составляющей, по сути, невозможно изготовить качественный композит. В чем причина? Из-за своих характеристик и консистенции древесная мука и полиэтилен не могут смешаться в однородную массу. Поэтому требуется дополнительное вещество, которое «запустит» реакцию между этими компонентами. К тому же с участием компатибилизатора в смеси не образуются комки, впоследствии изделие не будет разрушаться от влаги.
Для решения этой задачи используются добавки, в основе которых лежит малеиновый ангидрид. Это вещество токсичное. Поэтому при производстве ДПК такие добавки всегда идут в сочетании с ПНД. Их выпускают отдельные производители.
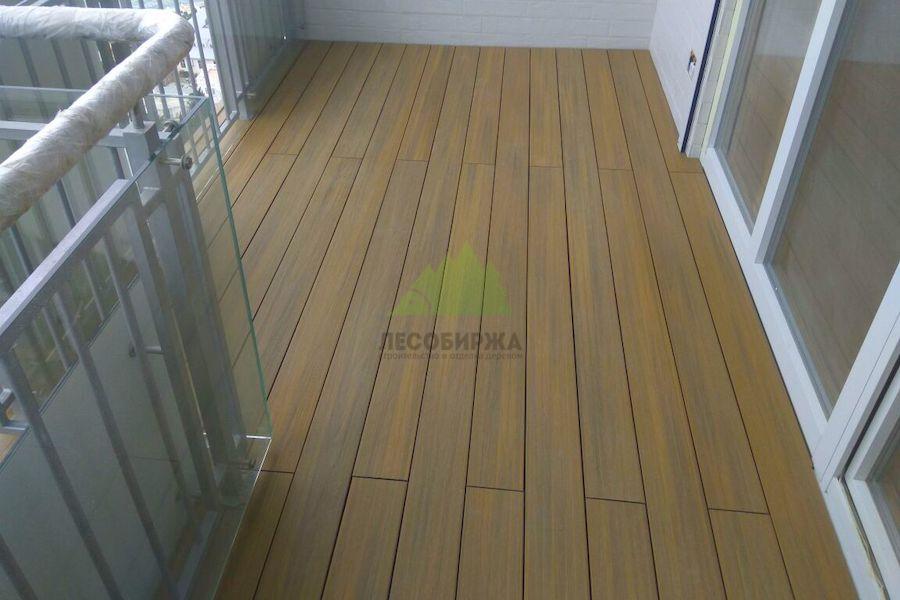
Фото 5. ДПК на балконе
Пигменты
Добавление пигментов (красителей) необходимо для того, чтобы придать изделиям из ДПК определенный оттенок. Очень часто производители используют железноокисные пигменты в виде порошка. Если нужно получить черный цвет, можно добавить в смесь технический углерод. Он дополнительно защищает панели от негативного влияния ультрафиолета.
Еще одна разновидность красителей носит название «мастербатчи». Это концентраты, выпущенные в виде гранул. Они открывают множество возможностей для окрашивания ДПК, однако стоимость их на порядок выше.
Большой выбор расцветок готового композита позволяет реализовать самые необычные идеи. Панели гармонично вписываются во многие стили и дизайны, будь то интерьерные или же ландшафтные работы.

Фото 6. Пол на балконе из декинга ДПК
УФ-стабилизаторы и антиоксиданты
Эти компоненты способствуют устойчивости досок к ультрафиолету и окислению, как на стадии производства, так и в ходе их использования. Обычно они составляют незначительную долю смеси. Отсутствие в ДПК антиоксидантов приводит к тому, что полиэтилен становится уязвимым и очень хрупким. Это значительно сокращает сроки эксплуатации доски.
Прочие добавки
В некоторых случаях в состав композита добавляют вещества, выполняющие дополнительные функции. Это могут быть:
- антипирены – повышают устойчивость изделия к воспламенению;
- биоцидные добавки – обеспечивают более мощную защиту от биологического повреждения.
Эти компоненты не являются обязательными. Иногда их эффективность даже подвергается сомнению.
Какие преимущества приобретает ДПК благодаря грамотному сочетанию всех перечисленных составляющих?
- Улучшенные прочностные характеристики в сравнении с натуральным деревом.
- Неизменность внешнего вида под воздействием осадков, ветра, ультрафиолета и перепадов температур.
- Материал легко поддается обработке, его можно многократно монтировать и демонтировать.
- Композит является универсальным. Его допустимо использовать в самых разных локациях, как в помещении, так и под открытым небом.
- За изделиями из ДПК не нужно по-особенному ухаживать. Они не нуждаются в регулярной шлифовке, лакировке или покраске. К тому же они служат долго без дополнительной обработки антисептиками.
Как видно, уникальный по составу продукт ДПК обладает массой достоинств, за это и пользуется спросом на рынке.
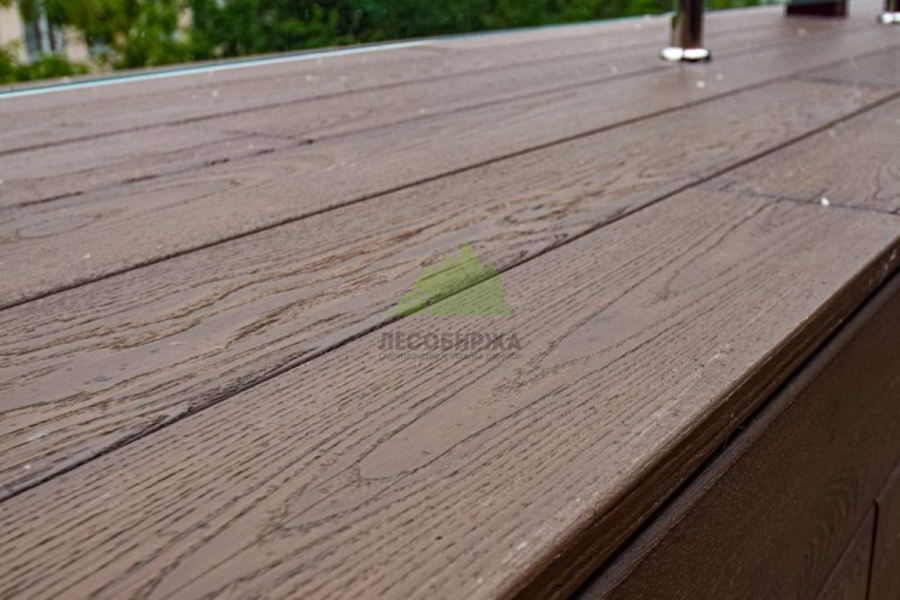
Фото 7. Ограждение террасы из ДПК
Технологический процесс
Исходя из приведенной выше информации можно сделать вывод, что процесс изготовления изделий из ДПК достаточно сложен. Хотя он полностью автоматизирован, это не исключает необходимость контроля обученным персоналом. Какие именно этапы включаются в технологию производства? Каким образом из отдельных компонентов получается готовый цельный продукт? Обо всех нюансах расскажут специалисты компании «ЛесоБиржа».
Смешивание
В процессе смешивания компонентов задействуется промышленный миксер. В зависимости от его конструкции и объема подготавливается замес – партия исходных компонентов определенного веса. Миксер состоит из верхнего и нижнего баков. Замес отправляется в верхний бак с герметичной крышкой. В этой емкости производятся одновременно и перемешивание составляющих, и разогрев смеси.
Стоит отметить, что нагревание способствует лучшему перемешиванию. К тому же при повышении температуры испаряется лишняя влага. Главные цели, которые достигаются в результате перемешивания:
- полностью расплавляется и смешивается с остальными веществами лубрикант;
- частично расплавляются гранулы полиэтилена.
Ход работ регулируется через пульт управления. Когда нагревание и смешивание выполнены, компоненты перемещаются в нижний бак. Эта емкость предназначена для охлаждения. За понижение температуры отвечает контур с водой. После охлаждения смесь фасуется в тару и отправляется в цех экструзии для следующего шага. Надежные производители знают, что в таком состоянии заготовки долго не хранятся, поэтому перерыв между двумя этапами минимальный.
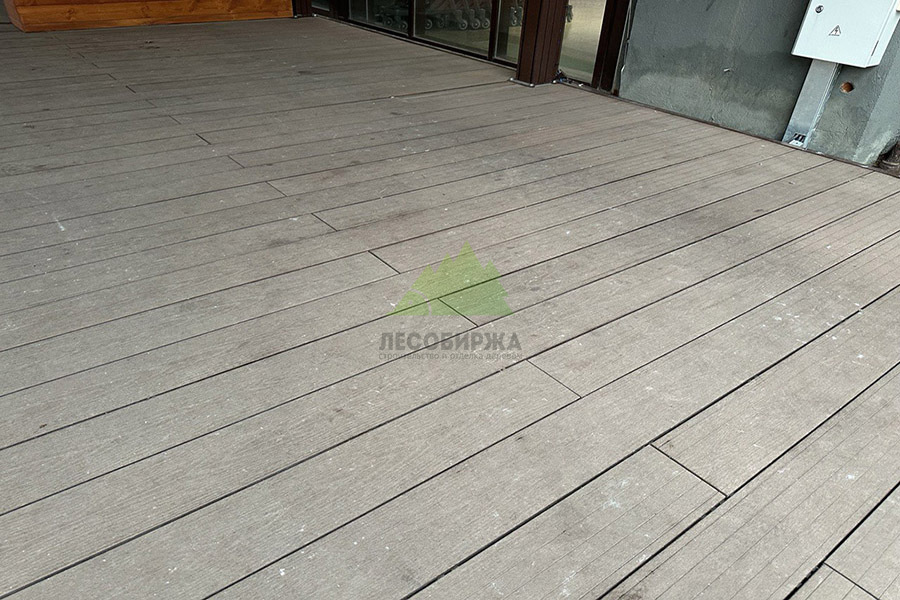
Фото 8. Терраса из ДПК от Лесобиржи
Экструзия
Это сложный многоступенчатый процесс, в результате которого получаются конечные изделия из ДПК. Как именно происходит экструзия?
Для ее осуществления нужны специальные станки – экструдеры. Если описать принцип их действия просто и коротко – он очень напоминает работу мясорубки. Станки оснащены вращающимися шнеками, которые выдавливают смесь в специальную форму, фильеру. Но на самом деле все далеко не так просто. Рассмотрим работу экструдеров более детально.
Первая часть экструдера носит название «пластификатор». Сюда загружается смесь. Пластификатор снабжен двумя шнеками, которые находятся внутри гильзы. Шнеки вращаются в одном направлении, а гильза в ходе работ нагревается. Нагрев осуществляется неравномерно, температура различается в разных частях. Таким образом обеспечивается пластификация смеси. Пластификатор – это именно то устройство, в котором все исходные компоненты, включая компатибилизаторы, перемешиваются и становятся однородной массой. Более того, в пластификаторе предусмотрены зоны удаления газов. Этот процесс необходим, иначе на выходе получится некачественное изделие с пузырящейся поверхностью и низким показателем плотности. После прохождения пластификатора смесь обретает консистенцию пластилина. Далее она попадает в основной экструдер.
Основной экструдер – это устройство с одним массивным шнеком. Проходя через него, смесь сжимается под высоким давлением и при определенной температуре. Затем аппарат выдавливает ее через фильеру, которая завершает конструкцию экструдера. Уровень нагрева и давления, а также скорость происходящих действий контролирует система управления.
Когда смесь пропускается через основной экструдер, она дополнительно разогревается. Степень нагрева не зашкаливает благодаря тому, что шнек в экструдере полый и дополнительно охлаждается водой, находящейся внутри.
Следующая стадия изготовления ДПК происходит в части, называемой «фильера». Она представляет собой металлическую конструкцию внушительных размеров, которая содержит множество пластин. Расплавленная смесь попадает в каналы, вырезанные в фильере. От их конфигурации зависит профиль будущих панелей – пустотелый или полнотелый. При этом благодаря нагревательным элементам обеспечивается температура, при которой расплав становится текучим. Однако, поскольку конечный продукт ДПК должен обладать твердой консистенцией, несколько завершающих пластин в фильере с интенсивностью охлаждаются водой. Нередко температура воды для охлаждения составляет всего 10-12 градусов.
Но на этом процесс не заканчивается. Выходя из фильеры, доска все еще пластичная, и ее легко повредить. Для придания изделию прочности оно помещается в калибратор. Он представляет собой металлическую конструкцию, в которой материал снова охлаждается. Проходя через калибратор, доска не подвергается такому же трению, как в фильере.
Для завершения технологии необходим еще один шаг. Калибратор направляет доску в просторную ванну с холодной водой. Здесь изделия из ДПК обретают свой окончательный вид и прочность. При выходе из ванны производится нарезка досок в соответствии с размером, и далее они укладываются в штабеля.
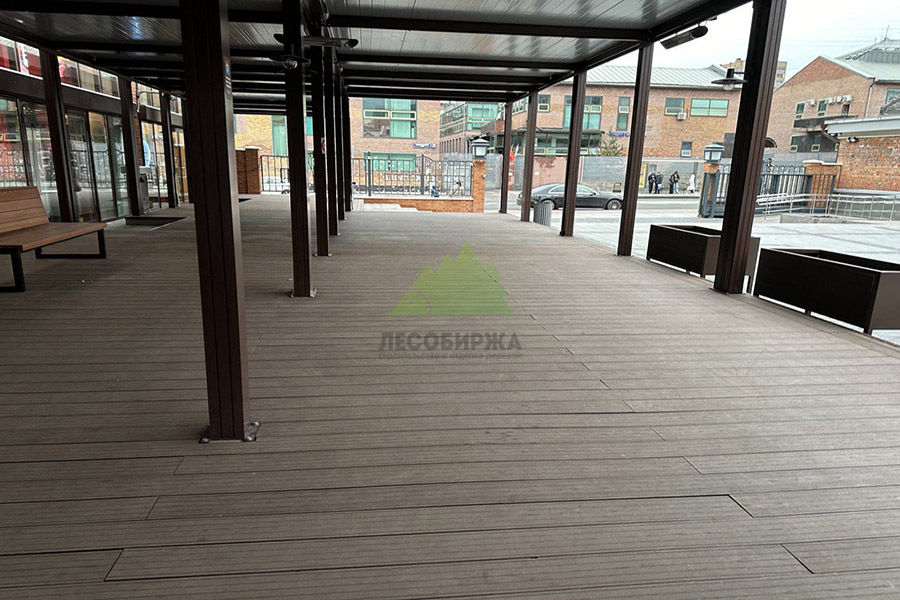
Фото 9. Шикарная терраса из ДПК от Лесобиржи
Брашировка
Проведение брашировки тесно связано с особенностями смазывающих компонентов. В процессе экструзии эти вещества перемещаются на поверхность доски и выполняют непосредственно свою задачу – облегчают продвижение смеси через фильеру. Когда профиль из ДПК остывает, лубриканты «превращаются» в тонкий слой воска на его поверхности. Это в некотором смысле улучшает эстетику панелей, но не очень хорошо для ее эксплуатационных характеристик. Такая поверхность сильно уязвима к царапинам и повреждениям, она склонна к выцветанию. Отсюда следует, что процесс брашировки крайне важен.
Как он производится? В ход идут металлические щетки. Они снимают с поверхности ДПК оставшийся воск и оставляют на изделии незначительные углубления. Благодаря такой обработке террасная доска из древесно-полимерного композита достойно выполняет свои функции даже под открытым небом. Незначительные повреждения, которые появляются на ней в ходе эксплуатации, не бросаются в глаза. Если необходимо добиться большей гладкости изделия, можно произвести шлифовку с использованием мелких абразивов.
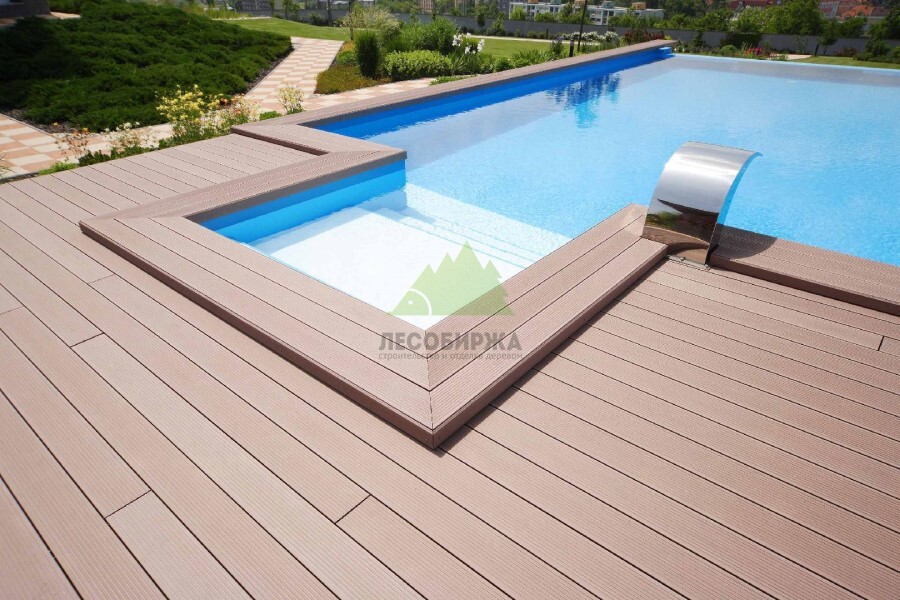
Фото 10. Площадка у бассейна из ДПК
Тиснение
Под тиснением подразумевается дополнительная обработка изделий из ДПК с целью придать им рельефную поверхность, которая будет имитировать натуральное дерево. Как это происходит?
Тиснильный станок имеет вид большого барабана. Изготовлен он из стали, а на его поверхность методом гравировки нанесен рисунок под древесную фактуру. Барабан нагревается, а доска под ним прокатывается, в результате чего на панели остается отпечаток рисунка. Чаще всего для этого используются полнотелые композитные доски.
Еще один вид обработки поверхности – это создание профиля «вельвет». Он подразумевает неглубокие продольные бороздки на лицевой стороне. Такая конструкция обеспечивает противоскользящие свойства настила и повышает безопасность передвижения даже в условиях осадков.
По сути, процесс изготовления ДПК на этом завершается. Но ответственные производители не упускают еще один немаловажный этап – лабораторные испытания. Почему они необходимы? Причина в том, что нарушения производственного процесса практически неизбежны. В подавляющем большинстве случаев опытный мастер определяет брак визуально, и сразу же налаживает работу линии. Но есть и ситуации (их не больше 5%), когда зрительно проблемы невозможно обнаружить. Тогда для выявления бракованной продукции и нужны лабораторные испытания. Благодаря им некачественный товар не поступает на склады и в продажу.
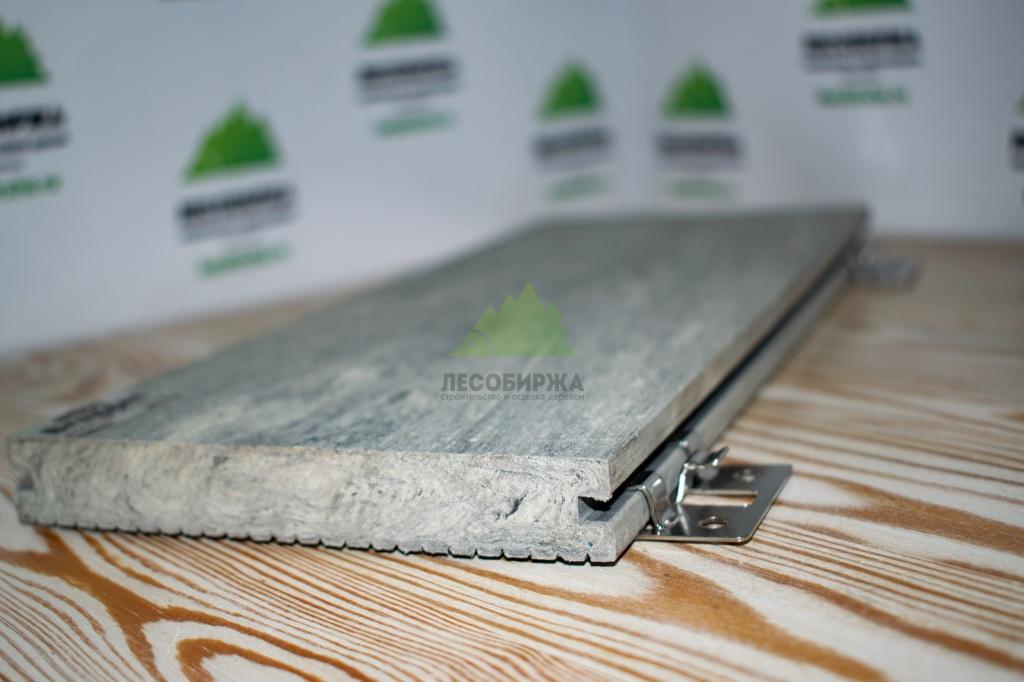
Фото 11. Террасная доска из ДПК
Какие именно показатели ДПК можно проверить в лаборатории?
- Точность геометрической формы изделия;
- плотность готовых панелей;
- влагостойкость и влагоотталкивающие свойства;
- прочность на изгиб.
По итогам лабораторных испытаний ДПК, не соответствующий нормативам, отправляется на переработку. Если же с панелями все в порядке, они отправляются на упаковку, а затем на склад.
Вывод: для изготовления композита с высокими эксплуатационными характеристиками нужна совокупность трех важных факторов – качественное исходное сырье, точно настроенное оборудование и квалифицированные работники.
Компания «ЛесоБиржа» ставит перед собой цель поставлять покупателю лишь высококачественные продукты из ДПК. На нашем производстве трудятся специалисты с достойным уровнем квалификации, и управляют они точным современным оборудованием. Обращаясь к нам, вы получите не только товары с гарантией качества, но и грамотное обслуживание. Наши мастера помогут вам в самых разных работах, связанных с оформлением вашей террасы. Все вопросы вы можете направить консультантам фирмы, связавшись с ними по указанным номерам телефонов. Мы с большим удовольствием выполним ваш заказ.